Key points of pipe fitting processing (III)
The brief introduction of key points of pipe fitting processing
8.Cutting process
Cutting is the process of finishing the welding end, structure size and shape tolerance of pipe fittings. The cutting of some pipe fittings also includes the processing of inner and outer diameters. Cutting is mainly accomplished by special machine tools or general machine tools. For large-sized pipe fittings, when the existing machine tools can not meet the processing requirements, other methods can also be used to complete the processing, such as gas cutting and grinding method for large-caliber elbows. The inspection of appearance and dimension of pipe fittings is usually carried out after cutting.
9.Nondestructive testing
Non-destructive testing is an important procedure for inspecting possible defects in the processing of materials and pipes. The requirements of NDT are stipulated in most pipe fittings product standards, but the requirements are inconsistent. In addition to non-destructive testing to meet product standards and order requirements, some manufacturers with stricter quality control also formulate non-destructive testing requirements based on material, processing technology and internal quality control regulations to ensure the quality of products.
In practical work, the qualified grade of non-destructive testing of pipe fittings should be determined according to the clear stipulation of order requirements or standards. Because the surface of the pipe is basically in the state of original pipe, plate or forging, for the nondestructive testing (MT, PT) of the surface quality of the pipe, if there is no definite grade requirement, it can be classified as Class II. However, no matter how the qualified grade is specified, the defects of sandwich and crack, which are not easy to determine the depth, should be regarded as unqualified. For non-destructive testing (RT, UT, etc.) of internal quality of pipe fittings, if there is no definite grade requirement, the radiographic testing should be level II (e.g. weld detection), and the ultrasonic testing should be level I.
In order to prevent possible defects in the product during heat treatment, the final non-destructive testing of the pipe should be carried out after heat treatment.
JB/T 4730 specification is commonly used in nondestructive testing of pipe fittings manufacturers in China. Personnel engaged in nondestructive testing shall be qualified in accordance with relevant provisions.
10.Surface protection
The surface protection of carbon steel and alloy steel pipe fittings is usually painted, and passivation of stainless steel after pickling is adopted (passivation is not necessary for all surface cutting stainless steel pipes). The main purpose of surface protection of pipe fittings is anti-corrosion, and at the same time achieve the effect of beautiful appearance of products. Usually, the orderer puts forward specific requirements for surface protection, and the manufacturer completes the surface protection of pipe fittings according to the requirements of the orderer.
11.Marking
Logo is an indispensable part of a product and the basis for achieving traceability requirements. In general, the content and method of the logo are specified in the product standard. The mark content of the pipe fitting generally includes the manufacturer's trademark or name, material grade, specification and other contents required for ordering. The method of marking includes permanent marking, such as steel seal, engraving, electroerosion, etc. Non-permanent mark, such as printing, label, etc.
12.In addition to the above conventional manufacturing process, in order to control the quality of raw materials, the manufacturer shall also complete the inspection of raw and auxiliary materials to ensure the correctness of the materials used; In order to meet the special requirements of ordering or materials, inspection and test should be carried out such as metallographic structure, intergranular corrosion, ferrite, etc., to ensure that the products provided meet the customer's requirements.
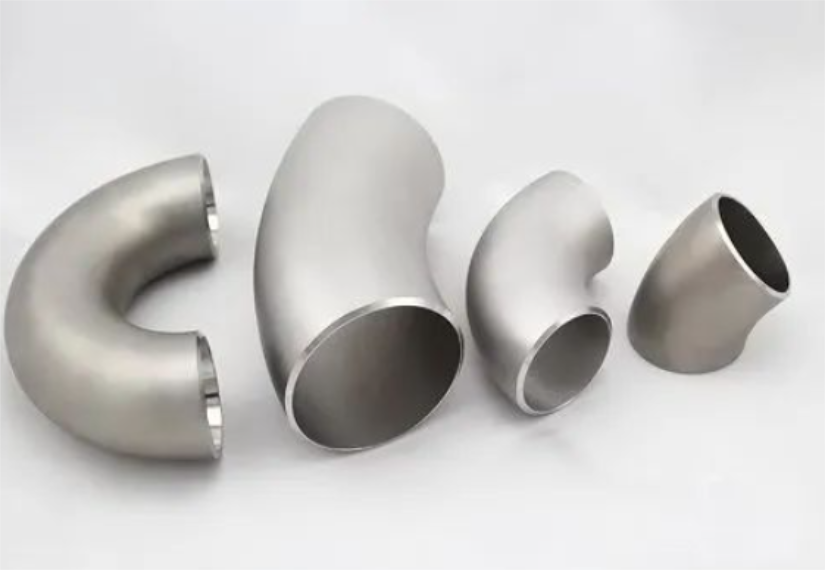