Technology of large diameter spiral steel pipe
This paper briefly introduces the production process of large diameter spiral steel pipe, which must pass rigorous physical and chemical inspection before joining. Wire or double wire submerged arc welding is used for end to end connection of strip steel, and self-submerged arc welding is used to repair after folding into steel pipe. Before setting, the strip is levelled, trimmed, planed, transported and treated with curved edges.
Production technology of large diameter spiral steel pipe
The electric contact pressure gauge is used to control the resistance of the hydraulic cylinder on both sides of the conveying to ensure the smooth transportation of the strip steel. The gap control system is used to ensure that the gap is considered in the welding regulations, and the welding machine is used to carry out long wire or double wire submerged arc welding for both internal and external welding, so as to obtain stable welding quality.
Welded gaps are verified by on-line continuous ultrasonic self-destructors, ensuring 100% non-destructive testing penetration of spiral gaps.
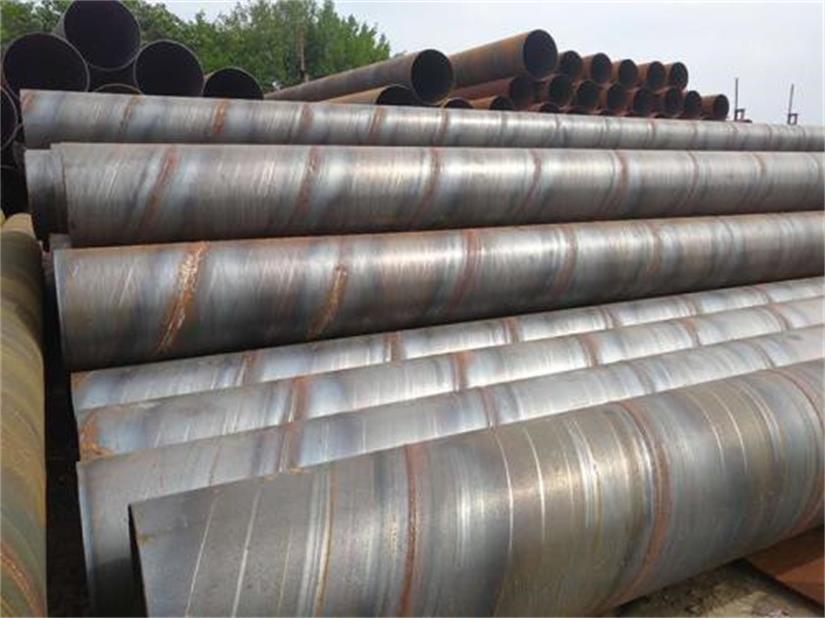
If there is a defect, the alarm and spray paint mark, processing staff to repair process specifications on time, on time to eliminate defects. The gas plasma cutting machine is used to cut the steel pipe into a single strip.
After cutting into a single steel pipe, each steel pipe must carry out a rigorous full inspection mechanism to verify the physical properties of the gap, chemical composition, fusion, the surface quality of the steel pipe and its non-destructive testing verification, to ensure that the pipe making process is up to standard, before it can really be added to the processing.
Where there is a continuous acoustic detection mark above the gap, it is reinspected by manual ultrasonic and X-ray, and if there is a defect, it is repaired and verified again by a non-destructive format until the defect is checked out.
The gap of the strip steel and the pipe to be combined with the spiral gap are all verified by filming, each steel pipe is tested by hydrostatic pressure, and the resistance is sealed radially.
The test resistance and duration are strictly controlled by the steel pipe water pressure microcomputer inspection assembly. Test specifications printed processing records. The tube end is machined for precise control of the vertical Angle, groove Angle and blunt edge of the port
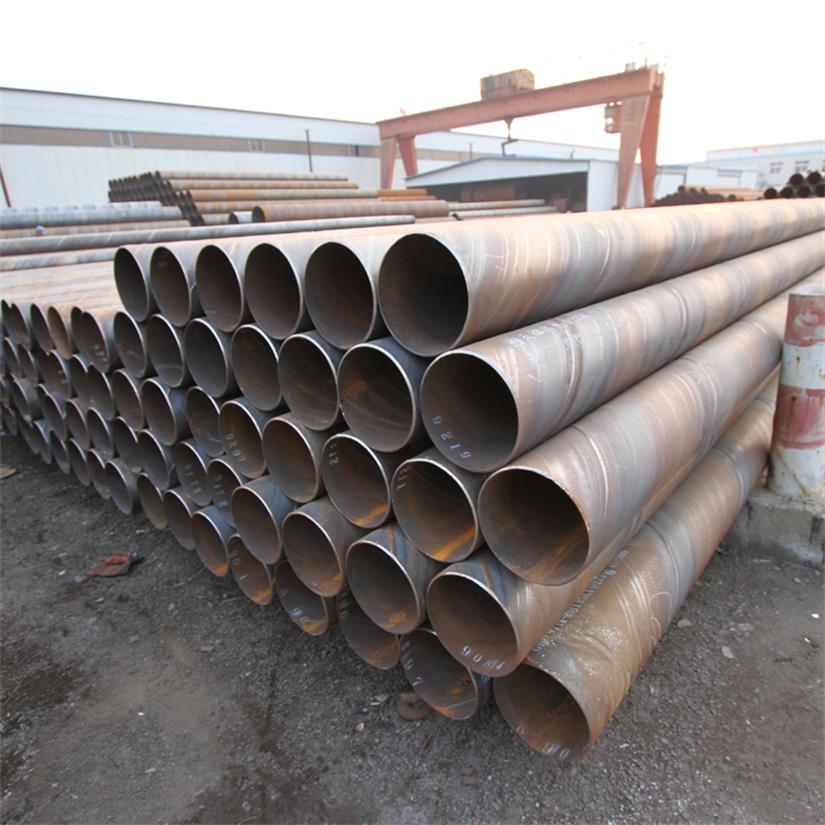
Factors that determine the quality of steel pipes
When large diameter spiral steel pipe is processed by different manufacturers, the introduced equipment and technology are different, and the quality and process of the factory will also have a very large gap.
Therefore, in the process of comparison, it will be found that the quality of the process sold by the manufacturer is higher in the market, and the recognition of customers will also be significantly improved. In general, in this comparison to reasonably grasp the quality requirements, so as to judge the quality gap.
In the processing of large diameter spiral steel pipe, surface treatment is an essential process.
In order to ensure that the quality of the steel pipe is strictly up to standard, the surface treatment needs to be more stringent at the factory to ensure the appearance quality and corrosion resistance, and the rust resistance and durability will be more and more prominent, so that the technical gap in all aspects is getting larger and larger, and the choice of customers will be different.